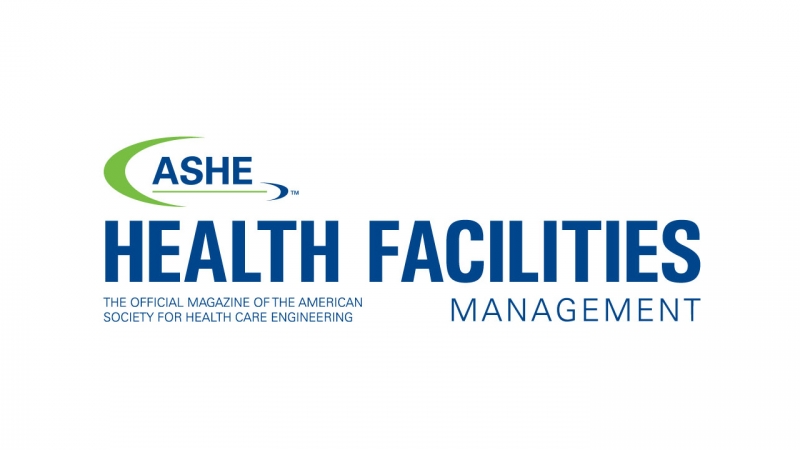
Facilities Metrics Help Drive Compliance
In a recent online issue of Health Facilities Management magazine, New York-Presbyterian’s (NYP) Sukhjit Tom Singh and Frank D. Rudilosso described how their organization harnesses data and technology to ensure safety and reliability across its sprawling 15 million-square-foot operation
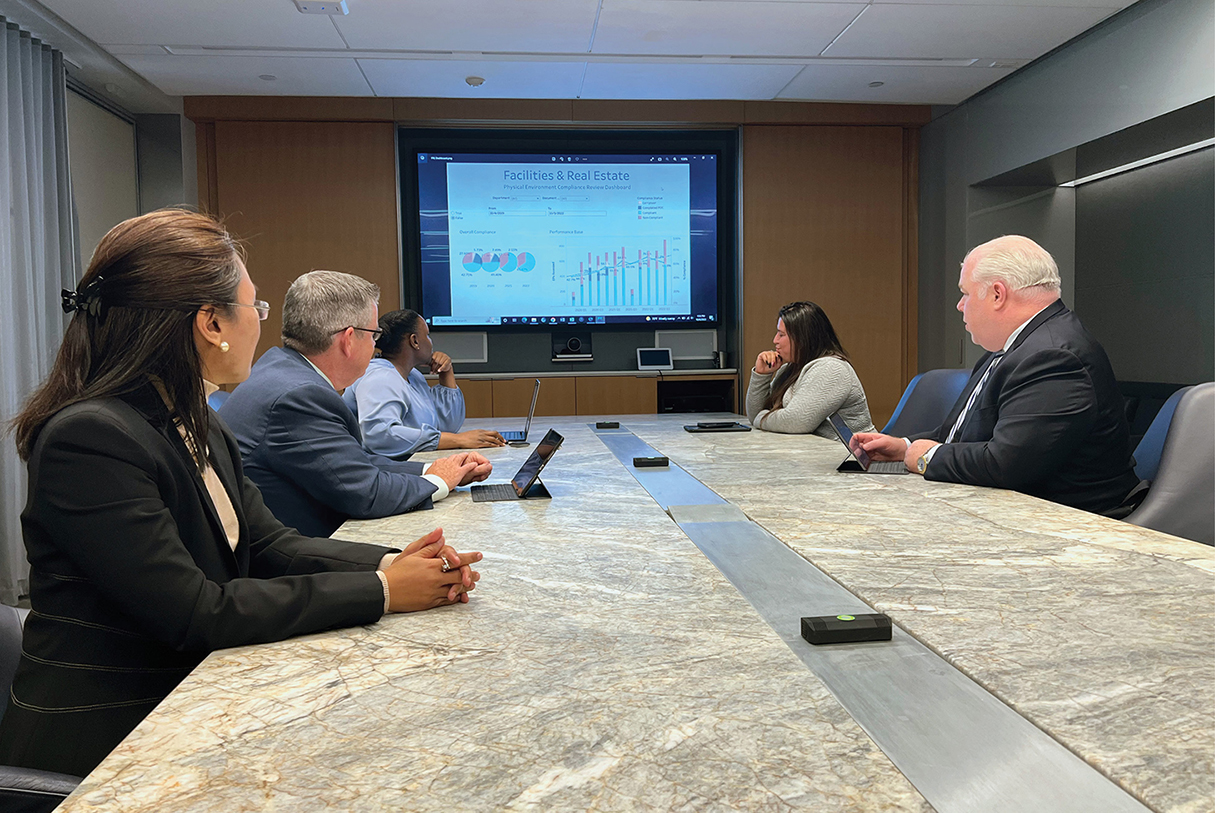
Members of NewYork-Presbyterian’s facilities operations, facilities operational excellence and environment of care compliance teams during a quarterly internal physical environment compliance documentation review.
As regulatory agencies and accrediting organizations continue to focus on the physical environment, data is becoming increasingly important for hospitals to maintain safe, reliable and compliant facilities.
NewYork-Presbyterian (NYP) offers a lesson in how other health care organizations can capture and utilize data to improve the safety and reliability of their facilities and systems.
A streamlined tool
As a large academic medical center with approximately 4,184 licensed beds consisting of 11 campuses and totaling approximately 15 million square feet, more than 500,000 inspection, testing and maintenance (ITM) activities occur on an annual basis.
NYP identified the opportunity of capturing facilities’ ITM data as well as physical environment risks into a streamlined reporting tool for leadership engagement and actionable results to reduce safety and compliance risks.
The overall approach involved various layers, including a transition to an electronic ITM reporting platform, conducting multidisciplinary rounds utilizing a graphical user interface (GUI) to identify risks, and developing a dashboard to track and trend compliance.
The objectives of the initiative include the following:
- Utilizing technology as a management tool to improve the overall patient experience, quality and safety.
- Engaging leadership through data-driven applications to improve operational efficiencies.
- Building a culture of accountability and ownership to achieve high reliability.
Data standardization
Like most initiatives in health care, the project didn’t happen overnight. NYP began the journey to improve their asset management program in 2011 after judging the existing program to be reactive and recognizing the need to develop an organized asset inventory that can be standardized across multiple sites. Identifying the many benefits to an organized asset inventory and the impact on maintenance and operations, NYP developed asset data standards.
The purpose of the asset data standards is to provide the facilities department and its vendors with standards and guidelines for maintaining facilities asset information, so that the data can support a robust maintenance and capital replacement program. The data standards include naming conventions and show how assets, procedures and preventive maintenance (PM) schedules are entered into the computerized maintenance management system (CMMS).
Barcoding standards identify the requirements for how barcodes should be applied for each asset type, who is responsible for collecting data at the end of a construction/renovation project and what system information should be tracked.
A data field document was developed that lists the fields that are typically collected for each equipment category. NYP uses asset categories to cluster tens of thousands of asset records into approximately 600 distinct equipment type groups. NYP uses a modified version of the UniFormat 2010 (Levels 1 to 4) classification system. This categorization helps to establish asset risk and ownership, and provides grouping for reporting and data analysis.
NYP developed an asset management committee to establish roles and responsibilities, processes and performance indicators. This group worked through the details of the asset management program to establish a reliable inventory, and to coordinate asset validations as well as a review of ITM procedures. This included a review of the capital planning process, proposed asset validation projects and regulatory requirements. The goal was to have a systematic and planned approach to asset management including standardizing nomenclature for systems, assets and procedures, planned validation projects and planned reviews of PM to get them handheld-ready and better able to track vendor performance.
Key features of the system include the following:
Ensuring confident results. NYP facilities systems, including CMMS, the data mart and its dashboard reporting, enable NYP’s teams to monitor its asset and ITM data and ensure that the data conforms to well-established asset and ITM data standards. Assets are all properly aligned with enterprise-level ITM programs. Shops and planners can effectively forecast, plan and schedule upcoming work, and facilities operations can maintain a state of survey-readiness by monitoring ITM schedule compliance and program performance.
CMMS reporting provides a forecast of PM work orders generated based upon next due dates. Work can be planned and scheduled allowing for lead times on labor, materials and vendor availability. The ITM program flowchart below identifies the steps taken from initial asset creation to activation of the PM program. It’s important to have quality control checkpoints and to identify areas of improvement, and allow for continuous improvements in the process.
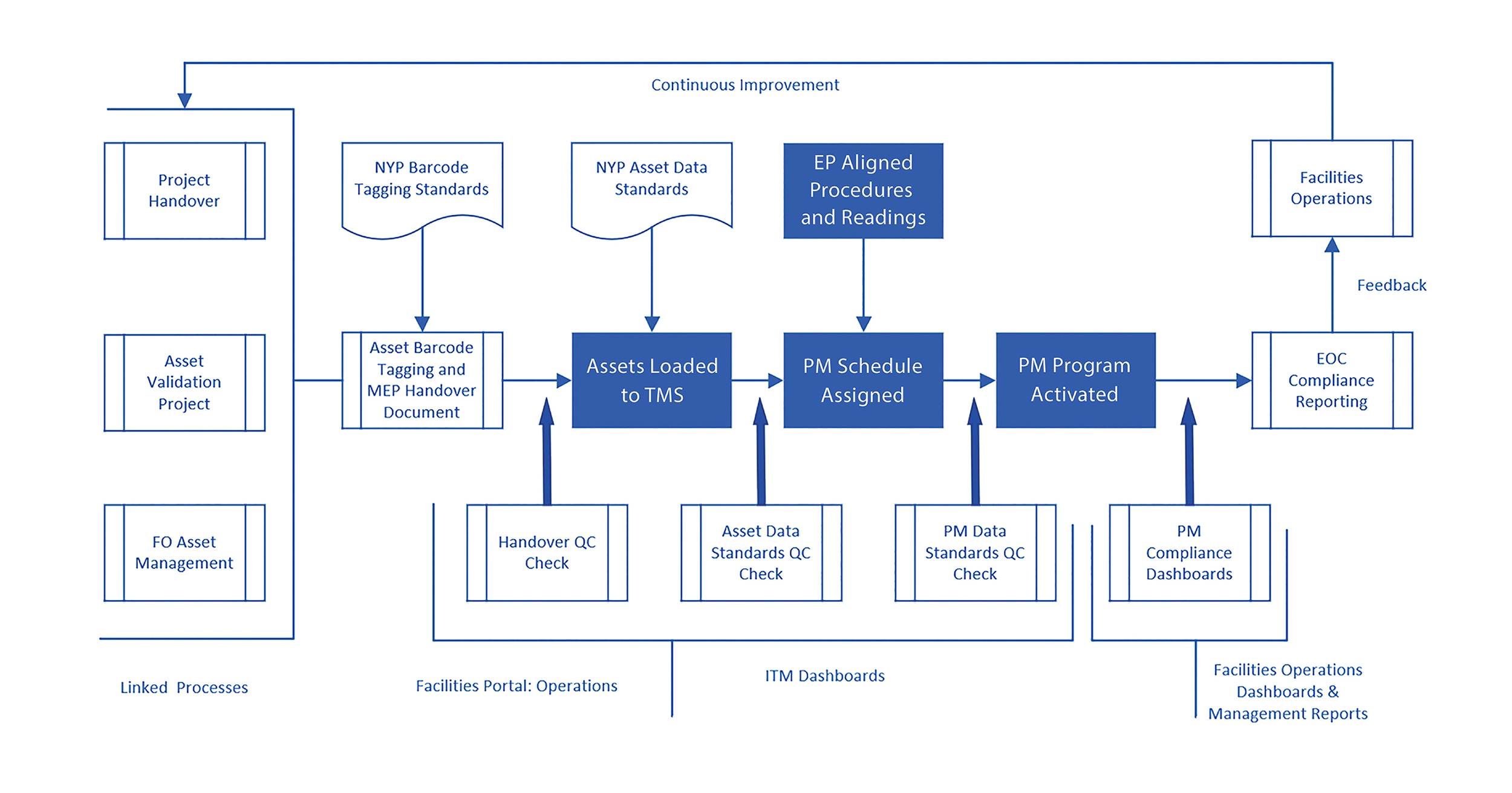
The ITM program flowchart identifies the steps taken from initial asset creation to activation of the preventive maintenance program.
Maintaining data integrity. Procedures were developed and associated with The Joint Commission’s (TJC’s) elements of performance. Procedure instructions were standardized per asset type and shared across campuses using standard libraries. To maintain the integrity of the data, NYP established dashboards to view assets added or updated in the past seven days. The dashboards also view whether assets, PM schedules and procedures are meeting NYP standards, and whether assets are on an ITM PM schedule.
This reporting allows the organization to have a simplified view to identify inconsistencies in the CMMS system. If an asset is not on a PM schedule, there is potential that it will not be inspected, tested or provided with the maintenance required on the appropriate frequency, putting the organization at risk of a regulatory finding. Dashboards are actively monitored by the facilities systems group with concerns communicated to the site’s CMMS coordinator or equivalent staff member.
Maintaining ITM compliance. Initially, NYP outsourced compliance document binder management to provide resources for the facilities teams to maintain compliance. To strengthen the collaboration, increase accountability and ownership, and support the facilities team with internal staff, NYP created a facilities operational excellence department.
NYP insourced compliance document binder management to staff the positions needed to provide the support. As part of the facilities operational excellence department, facilities regulatory compliance coordinators were hired. Their primary responsibility is providing support to the facilities operations team for regulatory compliance.
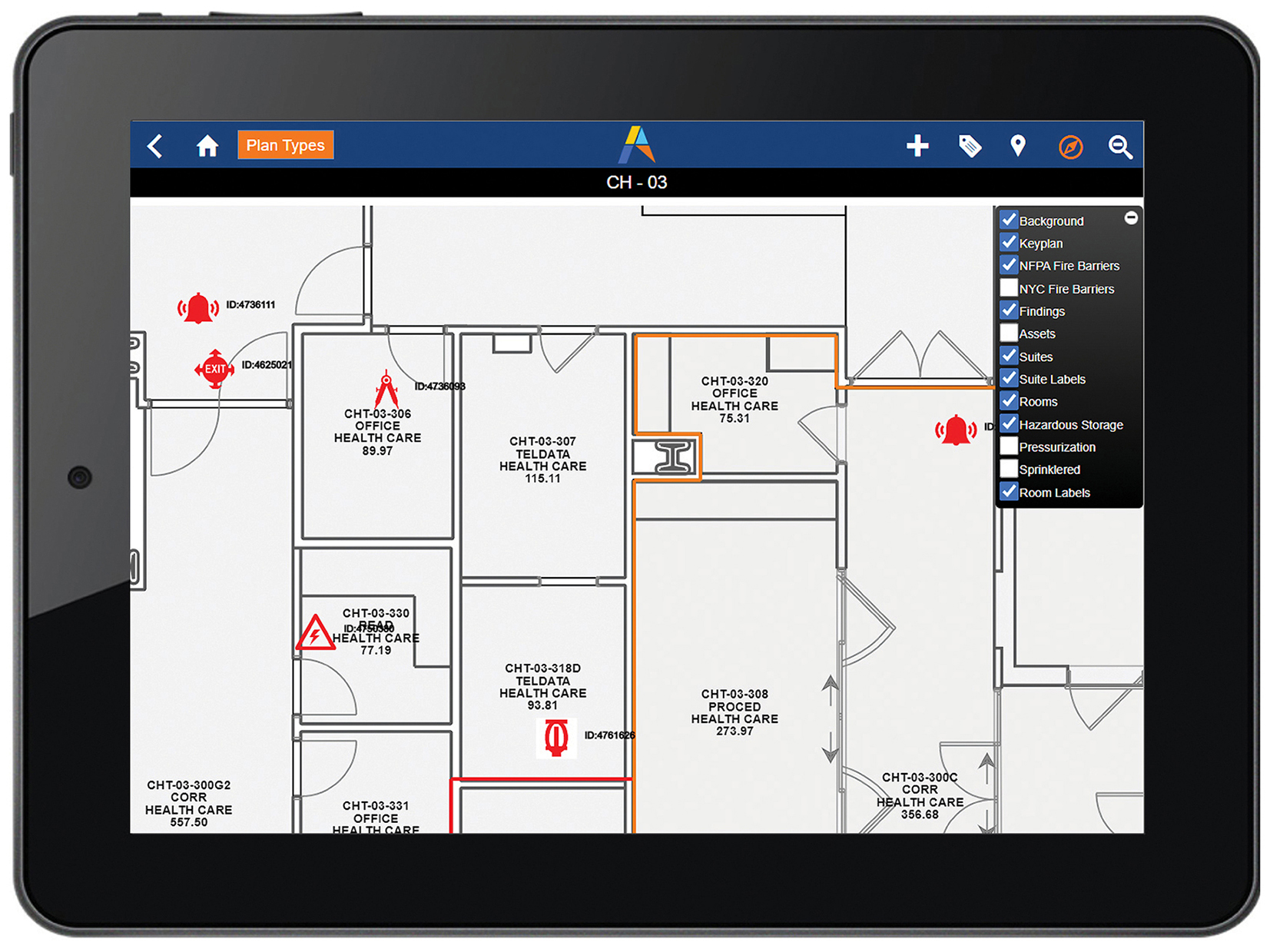
Risks identified with the building features are captured through a graphical user interface known as the visual asset management tool.
The compliance coordinators manage all regulatory documentation, review documentation to ensure compliance, and keep the documentation current in the electronic documentation system. This has improved the timeliness for updating the compliance information and ensures NYP maintains a constant state of readiness. In addition, this has allowed for the development of employees and potential movement within the organization.
The facilities compliance coordinators have the expertise and training to present the documentation during surveys in partnership with the facilities manager. This has provided more ownership and accountability for the process.
When coordinating the regulatory documentation, the compliance coordinators review documentation completed by vendors or in-house by facilities staff for adherence to all regulatory requirements and NYP standards. They develop standard templates, coordinate ITM activities and develop and track ITM activities required for TJC accreditation.
Electronic documentation. NYP replaced the physical compliance binders with electronic equivalents for web-based presentation to a surveyor or uploading to TJC’s website. At one point, TJC was conducting virtual surveys and required an organization to upload documents to the TJC portal. To be prepared for a virtual or on-site survey, NYP established a working group to develop a process to convert all paper documents to electronic.
This process included establishing a standard electronic content management folder structure as the repository for the compliance documentation, establishing a process for managing the repository and its file-folder structures and expanding the electronic management system, currently implemented for capital project archives and master drawings to manage compliance binders. NYP has an integrated approach in monitoring and maintaining compliance with the physical environment. This system was utilized during the most recent TJC survey and was deemed a best practice. It resulted in zero document review findings across all sites.
Internal audit process. There are multiple authorities having jurisdiction and regulatory agencies that have different requirements, which can make maintaining compliance very challenging. The NYP internal audit program, also called the “physical environment compliance reviews,” focuses on the most stringent regulatory requirements with an emphasis on the accreditation process.
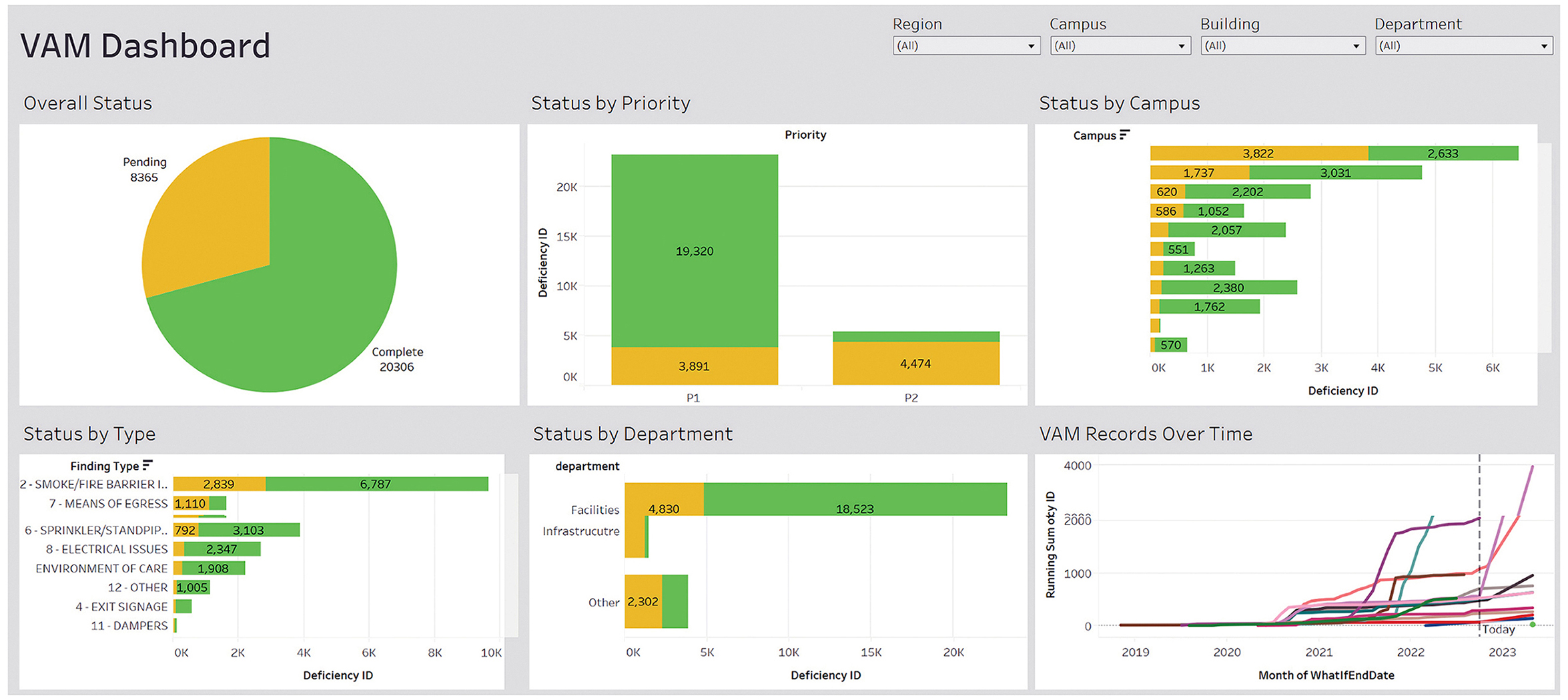
This dashboard allows the leadership team to view the observations related to the building features across each campus, by department responsibility and category type.
A corporate department called the “environment of care compliance team” conducts quarterly audits at each NYP campus, focusing on the physical building features as well as compliance with ITM documentation. Risks identified with the building features are captured using a GUI known as the visual asset management (VAM) tool.
Team members conducting the assessment all carry various tools including a tablet to document observations and view life safety building features, a vaneometer to check for air pressure relationships, a door gauge to assess for vertical and horizontal gaps, and a flashlight to assess above the suspended ceiling tiles.
The assessment also includes members of the facilities operations and engineering team to provide site-level support and resources to access spaces throughout the facility. In addition, ITM documentation is reviewed electronically with results captured in software called the “comprehensive online user compliance handbook” (COUCH) system.
The COUCH system interfaces with the VAM tool, which allows the system to incorporate all observations related to the specific audit event. The campus-specific report is sent to the site-level leadership team responsible for the physical environment within 10 business days from the last date of the audit activity. A plan of correction follow-up meeting is also scheduled approximately 30 days after the report has been sent to assess the status of the noncompliant observations. The dashboard is updated each day, with the data from the VAM tool and COUCH through the data mart, which contains all of the audit information.
The dashboard above allows the leadership team to view the observations related to building features across each campus, by department responsibility and by category type. This management tool provides leadership with an opportunity to allocate resources to proactively address existing conditions as well as reprioritize efforts to align with prevention strategies. The data is tracked and trended to show progress from quarter to quarter and year to year.
In addition, the dashboard below provides leadership with an overview of the overall compliance of the physical environment. This data set includes both building feature observations as well as items identified during the documentation review process. The dashboard allows the leadership team to drill down in terms of risk categories, campus-specific priorities and progress towards key targets and milestones.
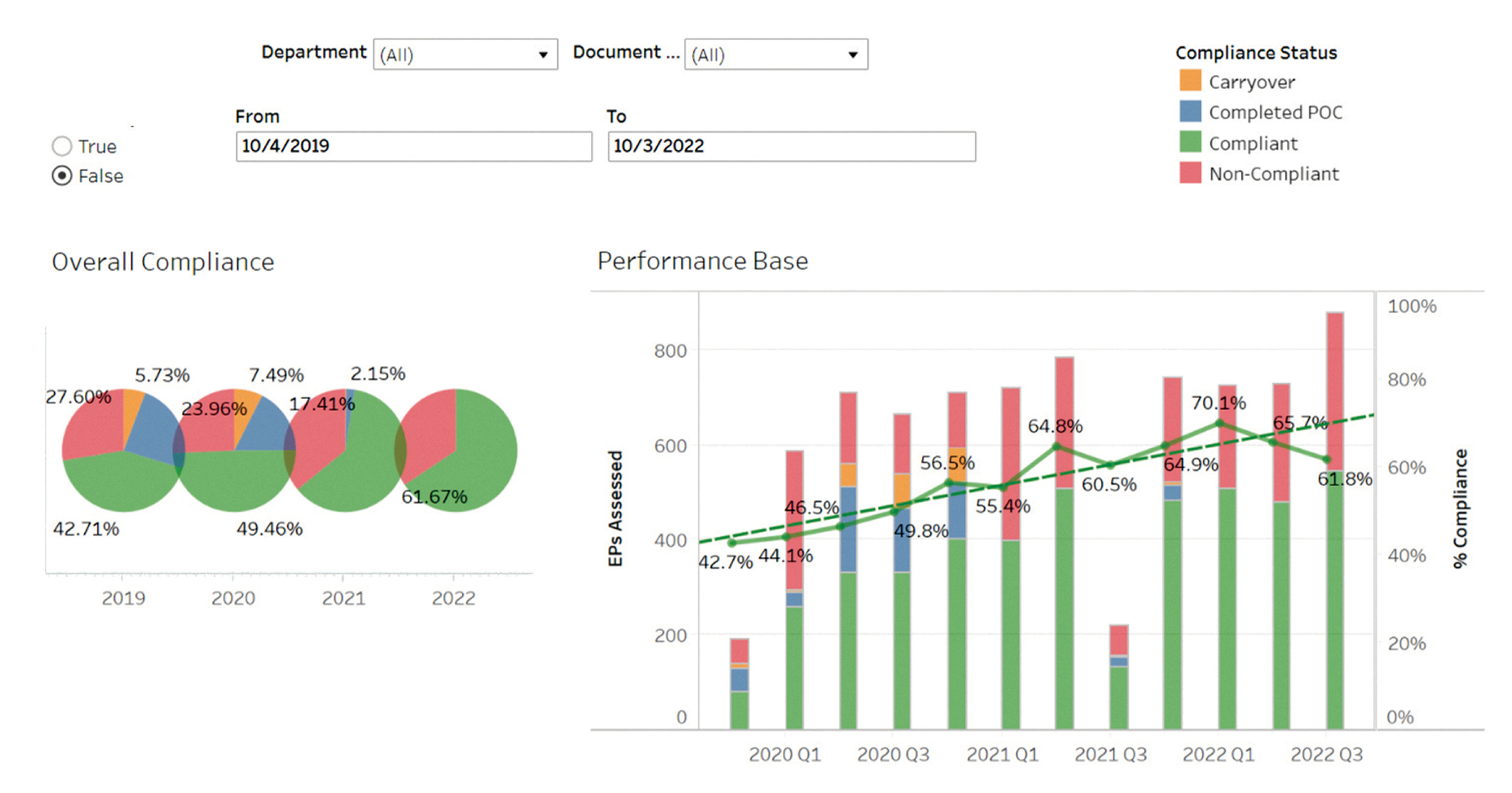
This review dashboard provides leadership with an overview of the overall compliance of the facilities and real estate physical environment.
Generating value
A systematic approach to data standardization generates value. By standardizing data and nomenclatures, organizations can simplify the maintenance of reliable building master records, simplify and streamline health care facility risk management and increase compliance with regulatory requirements.
NYP’s integrated approach to technology has dramatically improved management practices, streamlining the ITM reporting process with a structured outline and enabling access to reliable and real-time reports.
NYP’s goal of being a data-driven organization has greatly improved information quality. The results of this approach includes successful accrediting organization surveys across the NYP enterprise from July 2021 through April 2022 with minimal physical environment-related observations and no ITM documentation observations noted across the 11 NYP campuses. A constant theme during the accreditation survey process was the ability to standardize processes across 15 million square feet.
NYP was successful in achieving its objectives by utilizing technology as a management tool to improve the overall patient experience, quality and safety; engaging leadership through data-driven applications to improve operational efficiencies; and building a culture of accountability and ownership to achieve high reliability.
Developing a data-driven system for safety, reliability and compliance
To capture and utilize data to improve facility safety, reliability and compliance, health care organizations should start with the development of a data strategy for managing facility data. Once a structured inventory of facility elements is established, the organization can focus on optimizing operational processes, such as inspection, testing and maintenance; risk assessments; failure analyses; and handover of data from construction to operations.
An asset management committee can establish roles and responsibilities, processes and performance indicators. If the organization plans to move to electronic documents, the committee can develop a process to establish a standard electronic content management folder structure as the repository and a process for managing the repository and its file and folder structures.
For conducting internal audits, a team should be established and provided with necessary tools to identify and document observations in the field and during a document review. It should establish a frequency for conducting the internal audits and document the observations and document review findings in a system to allow the organization to track and trend the data that can be shared with leadership.
After conducting the internal audits, site leadership should develop and execute a plan of corrections for identified items to resolution. Effectiveness of the plan of corrections should be assessed during the subsequent internal mock audit. Overall results of the audits should be presented at the organization’s environment of care committee or equivalent forum on a designated frequency. Dashboards should be established to easily view and trend data to assist with recommendations for areas of improvement and to show progress to leadership.
To assist with development of a data strategy, the Health Care Facilities Management Data Nomenclature Standards worksheet can be downloaded from the American Society for Health Care Engineering (ASHE) website.
Supported by ASHE and the Facility Guidelines Institute, a group of health care professionals developed five classifications schemas for the following data sets: Buildings, Functional Areas (departments), Spaces, Building Systems and Building System Assets. These classification schemas are designed to provide health care planners, designers and operators with a common nomenclature.
Read the original article here: Facilities Metrics Help Drive Compliance
To learn more about digital transformation in health care